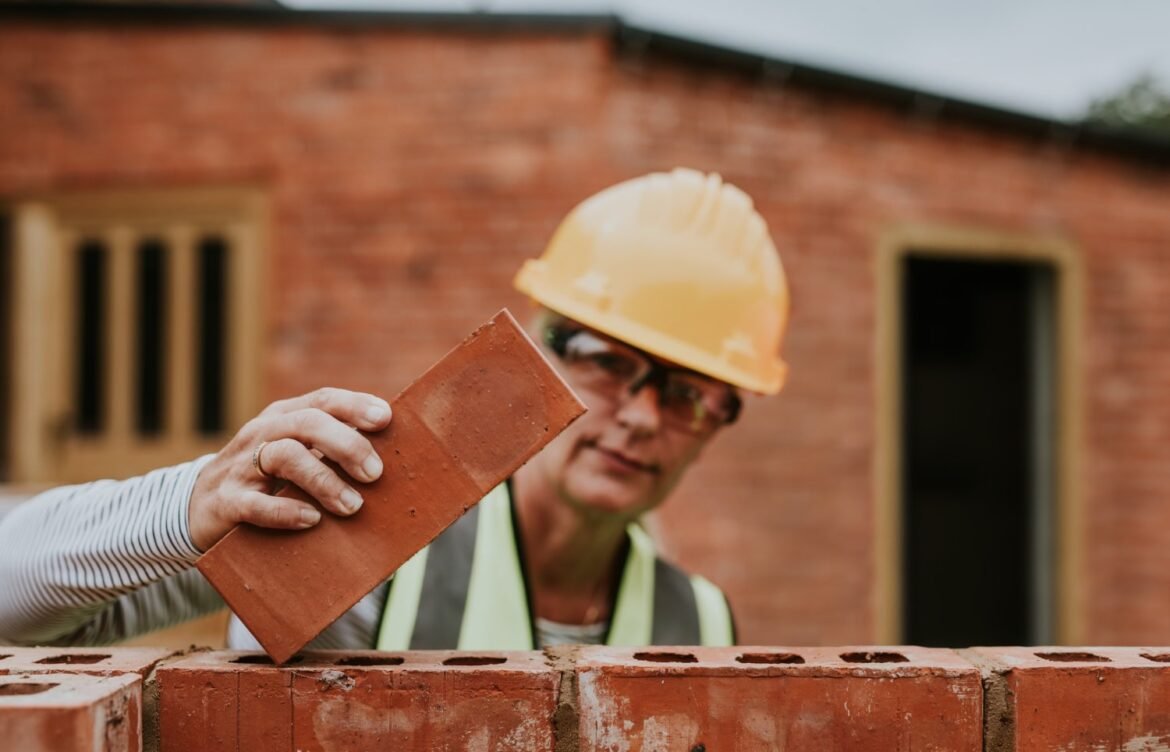
Construction Industry Struggles: Rising Material Costs and Supply Chain Disruptions
The past year has been a whirlwind for the construction industry. With demand for housing skyrocketing and contractors working at full capacity, the rising cost and shortage of construction materials have presented major challenges. Builders, homeowners, and developers are all feeling the pinch as prices for essential materials continue to rise.
Why Are Construction Material Prices Rising?
Several factors have contributed to the surge in material costs, making it difficult for builders to keep up with project demands and budgets.
Post-Pandemic Demand Surge
After COVID-19 lockdowns, the construction industry experienced a boom. Many homeowners who had postponed renovation plans during the pandemic rushed to complete their projects. At the same time, new home construction surged as demand for housing outpaced supply. This sudden increase in demand placed immense pressure on material suppliers, causing prices to climb rapidly.
Global Supply Chain Disruptions
The construction industry heavily relies on international supply chains for key materials like timber, steel, and cement. However, global shipping bottlenecks, port congestion, and factory shutdowns have created shortages. According to industry reports, the cost of timber alone increased by over 20% in the past year due to supply chain delays and rising transportation costs.
Labour Shortages and Inflation
Not only are materials in short supply, but the industry is also facing a labour shortage. A decline in skilled workers, combined with rising wages and inflation, has led to higher costs for builders. Many contractors have been forced to delay projects or adjust budgets due to the lack of available workers.
Impact on Homeowners and Builders
With costs on the rise, homeowners and builders are facing tough decisions. Construction companies are struggling to honor previous quotes as material prices fluctuate daily. A project estimated at $50,000 a few months ago may now cost significantly more, forcing homeowners to either increase their budgets or delay their projects.
How Homeowners Are Affected
- Higher costs for home renovations and new builds
- Increased competition for contractors and project delays
- Need to adjust budgets due to unpredictable material price hikes
How Builders Are Managing Costs
- Adjusting quotes frequently to account for price fluctuations
- Seeking alternative suppliers and materials to mitigate costs
- Passing additional expenses onto customers to maintain profit margins
Key Materials Experiencing Price Hikes
According to industry data, several critical building materials have seen significant cost increases:
- Timber and plywood – Prices surged due to global supply shortages and shipping delays.
- Steel – Increased global demand and limited production capacity have driven costs higher.
- Cement – Rising fuel prices and transportation costs have pushed cement prices up.
- Insulation materials – Supply chain issues and raw material shortages have led to delays and price increases.
What’s Causing These Supply Chain Issues?
Several global and domestic factors have contributed to ongoing supply chain disruptions in the construction sector:
Shipping and Freight Costs
Shipping container prices have soared, with reports indicating that freight costs have increased by over 500% in some cases. The high demand for materials and limited shipping capacity have created a backlog, delaying material deliveries and increasing costs for builders.
Shortage of Truck Drivers
The UK and many other countries are facing a shortage of HGV drivers. This has affected the delivery of essential materials, further slowing down construction projects. The issue has been compounded by Brexit-related labour shortages, with many European drivers unable to return to work in the UK.
Fuel Price Increases
With energy costs hitting record highs, fuel prices have surged, making transportation of materials more expensive. This has had a knock-on effect on nearly every stage of the construction supply chain, adding to overall costs.
How Contractors and Homeowners Can Adapt
Despite these challenges, there are ways to navigate the rising costs and supply shortages in the construction industry:
For Contractors:
- Update Quotes Regularly – Given the volatility in material prices, updating quotes frequently helps prevent unexpected cost overruns.
- Diversify Suppliers – Exploring alternative suppliers and materials can help reduce reliance on specific products facing shortages.
- Plan Ahead – Ordering materials in advance and securing fixed pricing where possible can mitigate the impact of price hikes.
For Homeowners:
- Increase Budget Flexibility – Expecting potential price changes can help prevent project delays due to unexpected costs.
- Consider Alternative Materials – Some substitute materials may offer cost savings without compromising quality.
- Be Patient – Supply chain issues are expected to persist, so planning ahead and allowing extra time for project completion is crucial.
Looking Ahead: Will Prices Stabilize?
While material costs have begun to stabilize in some areas, experts predict that supply chain disruptions and labour shortages will continue to impact the industry. It remains uncertain when prices will return to pre-pandemic levels, but industry professionals recommend keeping a close eye on market trends and adapting strategies accordingly.
The construction industry is facing unprecedented challenges, but with careful planning and adaptability, builders and homeowners can navigate these turbulent times. Whether you’re planning a home renovation or a large-scale construction project, staying informed about material costs and supply chain trends is key to making smart, cost-effective decisions.